Air Curtains For Environmental Cleanliness
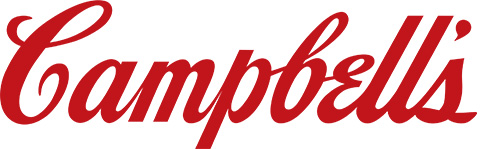
Challenge
The manufacturing environment demands stringent controls for safety, air quality, temperature, and cleanliness so that the work is performed within parameters for top performance. Campbell Soup Company, one of the largest food companies in the world with products in 120 countries, operates a sprawling, 2.4 million-sq.-ft. complex on a 949-acre parcel hugging the Maumee River in Ohio. Named as Food Processing Magazine’s 2014 Green Plant of the Year, this Campbell’s facility operates a cooler/freezer storage unit 24 hours/day alongside a 8’x16’ heavily trafficked forklift entrance with a fast-acting vertical-lift fabric door as part of an operation that crank out 107 million cases of soups, juices, beverages, and sauces each year. The hot, humid warehouse conditions collide with the cold, dry-storage area air which produces condensation and pools of water at the base of the freezer -- both inside and out. Pooled water also flows from the freezer opening directly into the walkways, interfering with both foot and forklift traffic.
The Solution
The Mars engineering team identified the precise area that needed an air stream to eliminate condensation, then installed a stack of vertically- mounted, door-activated air curtains and air diffusers* at the cold storage unit’s forklift entrance. The air curtain’s forced-air action stabilized cold area temperatures by creating an air seal which effectively evaporated most of the surface condensation, while also eliminating pools of water in the walkway. After effectively removing the center’s concerns, the Mars team went further and helped the facilities management team find solutions to condensation inside the freezer unit by recommending the air curtains operate with the door closed during low traffic conditions, and to use insulated material at the side walls.
STUDIES REVEAL A 6%-9% POSITIVE EFFECT ON WORK PERFORMANCE BASED ON IMPROVED AIR QUALITY AND TEMPERATURE. (WYON 2004)
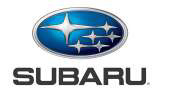
PRODUCING NON-TRADITIONAL SOLUTIONS
For high-value product manufacturers, controlling the plant environment and atmosphere within a narrow degree of variability means saving tens of thousands of dollars by eliminating defects. Both Subaru of America and TW Fitting NA, LLC, a BMW-contractor, used the Mars Air Systems air curtain to deliver a superior non-traditional solution for their manufacturing challenges. The Mars Engineering team’s solution helped prepare the tires that TW Fitting NA prepares for BMW vehicles by suspending electrically-heated air curtains over the tire conveyor belt. The curtains heated the tires just enough to create a more pliable rubber and eliminate the splitting, beading, and rim damage which had occurred with the colder rubber. The Mars solution also helped to lower energy costs by eliminating the need for an energy-gulping and unwieldy liquid-propane solution. Similarly, when Subaru needed near-pristine atmospheric conditions for their paint booths, Mars air curtains were installed in the hallway paint room entryway to act as a five-stage “air shower” for workers. Using the sequence of units, the Mars team was able to virtually eliminate dust and hair from the worker’s clothing so particles could no longer mar the painted finish.

MANAGING WIDE OPEN SPACES
Cavernous manufacturing centers grapple with complexities — numerous staff, high traffic, inconsistent climate control, and ongoing pressure to create productive working environments to hit output goals month after month. In the Campbell Soup Company’s sprawling, 2.4 million-sq.-ft. facility, an array of exterior doors continually introduce outside air into the workspace. Facility managers were using propeller-based fans in an inefficient attempt to block the unwanted airflow responsible for drafts and shrinking productivity. The fans were doubly ineffective because they used excessive horsepower to produce a wide flow of unfocused air. The Mars Air Systems air curtain solution was able to produce a precision air barrier with a concentrated blast of air that used only 3 HP versus the old system's 15 HP. Better still, the Mars solution completely eliminated the view obstruction of the fans while consuming the energy equivalent of one standard metal parking light with a 1500-watt metal halide bulb operating for one hour.

KEEPING IT FRESH ENOUGH FOR A BABY’S BOTTOM
P&G's Cairo plant, the third largest diaper plant in the world, responsible for exporting 60 percent of its production to Europe, Asia and the Mid- East, often leads as one of Egypt’s top American business success stories. Set in an area known for legendary dust storms that transfer accumulated debris from the far reaches of the Saharan Desert, air quality measurements routinely record dangerously high levels of suspended particulate matter. Mars Air Systems to the rescue. With the installation of over 100 Mars air curtain units in a plant hosting over 1200 workers, the result was an effective embargo on bad air and dust from blowing in at doorways and entryways. By deploying the Mars comprehensive facility-wide approach to controlling both loading dock entries and doorways with a directed stream of air, facility managers were assured that unpredictable climatic conditions would surrender to the power of the Mars air curtain and their invisible shield of protection.
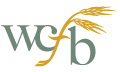
TOO MANY PEOPLE NEED US – IT HAS TO BE RIGHT
When you’re as successful as Westmoreland County Food Bank, you serve 7,200 families a month and operate a 40,000 sq.ft. facility that processes 8.6 million pounds of food a year - and your food storage equipment needs to work flawlessly. For Westmoreland, facility limitations forced the freezer and evaporator to sit side-by-side, which caused excessive humidity that led to ice and frost on the floor outside the freezer doorway – a safety hazard for both forklifts and workers on foot. When it’s too important or costly to be anything other than right, Mars Air Systems is the team you want on your side. Mars has been repeatedly the source for answers when large industrial and foodservice operators need no-fail solutions to vexing humidity, unwanted condensation, or hazardous pools of water. Deploying air baffles along side the series of air curtains gave the Westmoreland workers the means to ward off the flowing water that had been a source of slippage, falls, and worker injury.