Safe and Efficient Cold Storage with Air Curtains
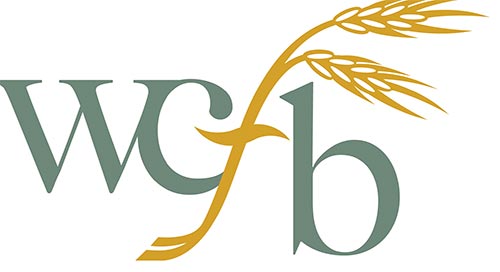
Challenge
When you operate a 40,000 sq.ft. facility that processes 8.6 million pounds of food a year is under your control, 7,200 families a month depend on you and 66 member agencies rely on you, you need your food storage equipment to work flawlessly to protect your most valuable property. And when you’re as successful as Westmoreland County Food Bank, growth demands action and new larger freezers. Food producers and distributors know that bad storage and handling can wreak havoc on their operation and that loading massive volumes of food into freezers is a meticulous process. For Westmoreland, facility limitations forced the freezer and evaporator to sit side-by-side which led to excessive humidity in the freezer, which in turn caused a build-up of ice and frost on the floor outside the freezer doorway – a safety hazard for both forklifts and workers on foot. All together these issues created a complexity that demanded the expertise of the Mars Air Systems engineering team to resolve.
The Solution
When it’s too important or costly to be anything other than right, Mars is the team you want on your side. Mars has been repeatedly the source for answers when large industrial and foodservice operators need no-fail solutions to vexing humidity, unwanted condensation or hazardous pools of water. Deploying air baffles along-side the series of air curtains in the food bank gave the Westmoreland workers the means to ward off the flowing water that had been a source of slippage, falls, and worker injury.
STUDIES REVEAL A 6%-9% POSITIVE EFFECT ON WORK PERFORMANCE BASED ON IMPROVED AIR QUALITY AND TEMPERATURE. (WYON 2004)
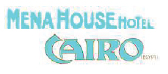
PRODUCING NON-TRADITIONAL SOLUTIONS
To make sure frozen food keeps its sensory and nutritional quality, as well as maintain food safety standards, temperature requirements have been set for every stage of the cold storage chain. No less a consideration is the hit to food storage life when products are exposed to temperature fluctuations. In challenging environments, the mere act of moving food from a transport truck to a freezer can raise the temperature of the food significantly and tax a cooling system as it struggles to return to the thermostat set point. The Mena House Hotel in heat-steeped Cairo, Egypt has welcomed dignitaries such as Winston Churchill, Queen Mary and Richard Nixon as well as average summer temperatures of 94°F to 104°F. With a bank of 20 foot by 20 foot freezers that needed frequent stocking to keep hotel guests fed, a significant solution was needed to unburden the freezer compressors, protect the food from heating up, and give some relief from rising energy costs. Using a series of 42-inch custom-engineered models, the Mars Air Systems engineering team was able to create a wall of cold air to halt the incursion of heat and dust. The air curtains eliminated temperature fluctuations, reduced the stress on the equipment, and helped reduce burgeoning energy costs.
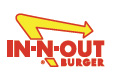
TOP CHAINS ORDER UP PEAK PERFORMERS
While a Health Department code may prescribe air curtains to create cleaner, pest-free food prep areas, the real mandate comes from patrons. Creating a pest-free space with evenly-distributed conditioned air does more than give guests the impression of cleanliness, it’s actually a building block to designing a truly hygienic venue. Food poisoning is directly linked to flies who carry pathogenic organisms that cause E. coli, salmonella, and shingles, and introduce other bacteria. Working hand-in-hand with the sanitation protocols you already have, Mars Air Systems’ air curtains above entry doors, pass through windows, and back receiving doors become silent sentries that seize control to keep out the uninvited. We’ve been doing that for over 50 years for iconic hospitality brands such as Panda Express, In-N-Out Burger, Taco Bell, Subway, and Olive Garden as well as growing up-and-comers like Smashburger and Five Guys Burgers. Whether you need a recessed unit that blends seamlessly with a well-defined décor, or defense against brutal weather conditions (hot or cold), or vigorous defense for food storage areas, Mars products have been the solution of choice for the most demanding operators world-wide.
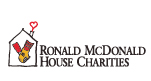
WHEN A SOLUTION WORKS THIS WELL…ADD ANOTHER
Sometimes the challenge is less a problem and more an opportunity to repeat what already works well. When Camp Ronald McDonald for Good Times in Southern California unveiled a new dining hall in 2015 to significantly enhance the camp experience for youth struggling with cancer and their families, it opened with two donated Mars Air Systems air curtains standing guard over their foodservice delivery doors. For the staff, finding a solution meant having to look no further than the wall in the existing dining hall, where they found a circa-1989 Mars air curtain still hard at work in the retiring dining center. The 26-year old unit was still faithfully creating the wall of air needed to repel exterior air and dispel dirt, dust, and insects. Happy to be able to keep the still-operating air curtain in place as the outmoded facility transitions to a culinary teaching center, the staff reached out to Mars for two additional workhorses. The Mars contribution joins the ranks of built-environment leaders such as HunterDouglas and Dupont™ Corian® to breathe life into the new 14,000 square foot complex so guests can recreate the family dining table while at camp.

PUTTING THE SKIDS ON SLIPPERY
Campbell Soup Company, one of the largest food companies in the world, operates a sprawling, 2.4 million-sq.-ft. facility on a 949-acre parcel, which includes operating a cooler/freezer storage unit 24 hours/day alongside a 8’x16’ heavily trafficked forklift entrance with a fast-acting vertical-lift door. The hot, humid warehouse conditions collide with the cold, dry-storage area air which produces condensation and pools of water at the base of the freezer -- both inside and out. Pooled water also flows from the freezer opening directly into the walkways, interfering with both foot and forklift traffic. The Mars engineering team identified the precise area that needed an air stream to eliminate condensation, then installed a stack of vertically- mounted, door-activated air curtains and air diffusers* at the cold storage unit’s forklift entrance. The air curtain’s forced-air action stabilized cold area temperatures by creating an air seal which effectively evaporated most of the surface condensation, while also eliminating pools of water in the walkway.