Air Curtains For Work Cleanliness
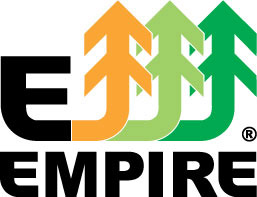
Challenge
Challenged to find ways to differentiate in the extremely competitive corrugated packaging marketplace, this leading producer deploys the Mars Air Systems air curtain solution to contribute to a cleanliness standard that helps them pass the most stringent audits and sets them apart from other food casing providers.In a 62,000 sq. ft. facility, Empire Packaging and Displays produces $50M annually in corrugated boxes and power wing displays, which give food producers the means to package, ship, and display their products in the hygienic envelopes that are in demand in today’s highly-regulated food safety environment. Once a user of plastic strips to guard their dock doorways, the Empire team realized “plastic strips were the number one hazard in the factory – even more than the equipment we used,” said co-owner Hal Mottet, “because they were constantly dirty, had turned cloudy after a month of use, and were often pushed aside by staff who found them cumbersome and intrusive to their work.” The Empire team quickly recognized that for a few dollars in electricity per month they could achieve a safe and effective barrier to keep dust, debris, and flying insects out of the plant with the added bonus of more productive climatic conditions for workers.
The Solution
After years of struggling to function well and work amid the “rules” the staff had put into place to avoid injuries with the tangled and visibility-reducing plastic strips, Empire put safety first by installing three 14-foot dock door Mars air curtains.“On hot days the plant definitely feels cooler with the Mars units riding shotgun over the dock doors. Neither shift is using makeshift methods to move the plastic strips out of the way now that they’re gone and visibility around the dock doors is at all-time highs which eliminates our worries about worker safety. The American Institute of Baking International (AIB) agrees that the Mars air curtain solution is far superior and helps us meet the cleanliness standards so we can pass their rigorous audit year after year,” says Mottet. “And having that credential from AIB is instrumental to many of the clients we serve and one we consider critical to our continued success.”
“THE PLASTIC STRIPS WE USED IN THE PAST WERE SIMPLY UNSAFE AS ALL GET OUT,” HAL MOTTET, EMPIRE PACKAGING AND DISPLAYS CO-OWNER

KEEPING IT FRESH ENOUGH FOR A BABY’S BOTTOM
P&G's Cairo plant, the third largest diaper plant in the world, responsible for exporting 60 percent of its production to Europe, Asia and the Mid- East, often leads as one of Egypt’s top American business success stories.Set in an area known for legendary dust storms that transfer accumulated debris from the far reaches of the Saharan Desert, air quality measurements routinely record dangerously high levels of suspended particulate matter. Mars Air Systems to the rescue. With the installation of over 100 Mars air curtain units in a plant hosting over 1200 workers, the result was an effective embargo on bad air and dust from blowing in at doorways and entryways. By deploying the Mars comprehensive facility-wide approach to controlling both loading dock entries and doorways with a directed stream of air, facility managers were assured that unpredictable climatic conditions would surrender to the power of the Mars air curtain and their invisible shield of protection.
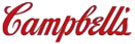
PUTTING THE SKIDS ON SLIPPERY
Campbell Soup Company, one of the largest food companies in the world, operates a sprawling, 2.4 million-sq.-ft. facility on a 949-acre parcel, which includes operating a cooler/freezer storage unit 24 hours/day alongside a 8’x16’ heavily trafficked forklift entrance with a fast-acting vertical-lift door.The hot, humid warehouse conditions collide with the cold, dry-storage area air which produces condensation and pools of water at the base of the freezer -- both inside and out. Pooled water also flows from the freezer opening directly into the walkways, interfering with both foot and forklift traffic. The Mars engineering team identified the precise area that needed an air stream to eliminate condensation, then installed a stack of vertically-mounted, door-activated air curtains and air diffusers* at the cold storage unit’s forklift entrance. The air curtain’s forced-air action stabilized cold area temperatures by creating an air seal which effectively evaporated most of the surface condensation, while also eliminating pools of water in the walkway.

CONTROLLING HUMIDITY TO MANAGE DEFECTS
Uncontrolled relative humidity levels in manufacturing can damage products during production and strike a blow to the top line.At Illinois-based Schrock Cabinetry's 1M sq. ft laminated cabinet plant, dozens of expansive loading dock doors and entry doors gave rise to an unwinnable cat-and-mouse game as plant operators tried to keep plant temperature and humidity stable so the laminated finish didn’t crack. Knowing Mars has repeatedly provided the right answer when large industrial operators need no-fail solutions to vexing humidity, condensation, or pooling water, the Schrock team installed a series of air curtains of their own. The units now stand guard and help create consistent climate conditions so production teams can focus on making the semi-custom cabinets that have given them a national reputation.
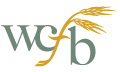
TOO MANY PEOPLE NEED US – IT HAS TO BE RIGHT
When you’re as successful as Westmoreland County Food Bank, you serve 7,200 families a month and operate a 40,000 sq.ft. facility that processes 8.6 million pounds of food a year - and your food storage equipment needs to work flawlessly. For Westmoreland, facility limitations forced the freezer and evaporator to sit side-by-side, which caused excessive humidity that led to ice and frost on the floor outside the freezer doorway – a safety hazard for both forklifts and workers on foot. When it’s too important or costly to be anything other than right, Mars Air Systems is the team you want on your side. Mars has been repeatedly the source for answers when large industrial and foodservice operators need no-fail solutions to vexing humidity, unwanted condensation, or hazardous pools of water. Deploying air baffles along side the series of air curtains gave the Westmoreland workers the means to ward off the flowing water that had been a source of slippage, falls, and worker injury.